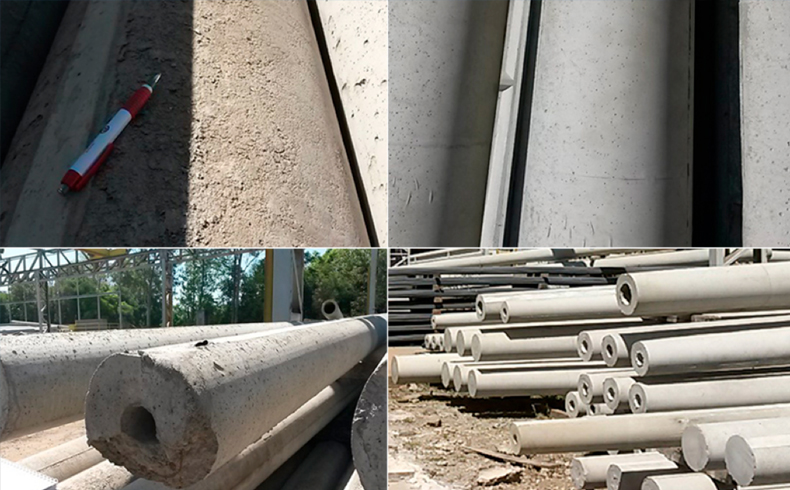
CAA garante alta resistência inicial e final na produção de pré-fabricados
Implantado em duas indústrias do Rio Grande do Sul, o concreto autoadensável se destacou por aumentar a produção em 30% e reduzir a jornada de trabalho em 25%
Fornecendo tecnologia de ponta e suporte técnico a seus clientes a Votorantim Cimentos implantou o concreto autoadensável (CAA) em duas indústrias de pré-fabricados do Rio Grande do Sul. A ação foi coordenada pela Engenheira Jadna Fuchter, responsável pelo Desenvolvimento Técnico de Mercado da Votorantim Cimentos que contou também com a consultoria do Prof. Dr. Bernardo Tutikian, coordenador do itt Performance.
Desafio
O concreto autoadensável precisava apresentar resistências inicial e final superiores aos números atingidos pelo concreto convencional (CC), conforme as exigências das indústrias onde foi implantado.
Especialista em postes de linhas de transmissão, a indústria 1 carecia de um concreto com resistência entre 15 MPa e 20 MPa nas primeiras 24 horas, e de 35 a 40 MPa aos 28 dias. Já a indústria 2, que trabalha com pré-moldados, precisava de um material que também garantisse de 35 MPa a 40 MPa aos 28 dias.
Solução
Na indústria 1, o concreto convencional atingiu 10,2 MPa de resistência à compressão nas primeiras 24 horas, contra 15,8 MPa do concreto autoadensável (número 50% maior). Depois de 28 dias, o CC foi novamente superado – desta vez em 40% –, pois apresentou apenas 44,7 Mpa, enquanto o CAA alcançou 64,3 MPa.
Os resultados na indústria 2 foram mais parecidos: nas primeiras 24 horas o CC apresentou 17,9 MPa e o CAA 19,4 MPa – quase 10% maior. Porém, após 28 dias, os resultados voltaram a apresentar uma diferença considerável: o concreto convencional teve pico de 35,2 MPa frente aos 44,2 MPa do concreto autoadensável – 25% maior.
O CAA utilizado nas duas indústrias do Rio Grande do Sul contou com um pequeno acréscimo de argamassa seca, aditivo superplastificante, e um aumento na quantidade de materiais finos para evitar a segregação dos sólidos em suspensão na mistura.
As composições foram testadas em cada indústria visando pequenos ajustes conforme as necessidades de cada uma. Em ambos os casos, foi possível reduzir o consumo de cimento no traço do concreto autoadensável, tornando-o ainda mais competitivo com o concreto convencional.
Benefícios
Mais fluido, o concreto autoadensável escoa através do seu próprio peso e preenche as formas sem riscos de segregação. Nas duas indústrias citadas, ele aumentou a produção em 30% e reduziu a jornada de trabalho em 25%. Além disso, os colaboradores foram remanejados para outras funções, otimizando a mão de obra da indústria
Diferente do convencional, o material é menos danoso às formas e ao conjunto de pás dos misturadores. Inclusive, reduziu a necessidade de manutenção periódica e a substituição parcial ou total dos equipamentos usados para misturar o concreto.
A etapa de adensamento mecânico por vibração foi desativada nas duas empresas, diminuindo os ruídos no interior das fábricas e o consumo de energia elétrica. Embora estas características não tenham sido mensuradas, estudos anteriores demonstraram haver uma redução no nível de ruído de cerca de 20 dB para este tipo de alteração, melhorando as condições de trabalho dos operários.
Outra vantagem foi a baixa necessidade de reparos no produto final, pois o CAA garante melhor acabamento das peças. A solução também gerou poucos resíduos, o que facilitou a limpeza das formas e vem também contribuindo com o meio ambiente.
Confira também como o concreto autoadensável mostrou-se a solução mais ágil e econômica para o Residencial Allegro.